You are here: Home » Why Choose Water Jet Cutting
Why Choose Water Jet Cutting?
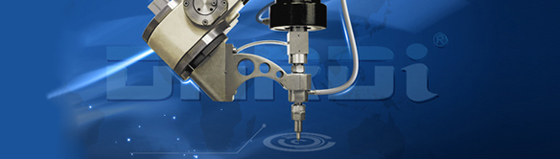
Waterjet cutting machine is a tool that can slice metal or other materials into pieces by ejecting a jet of water at high velocity and pressure. It is often used for manufacturing machinery components. Waterjet cutter is an ideal product for materials which are sensitive to high temperature during the cutting process. Waterjet cutting machine has wide applications in many industries, such as automobile manufacturing, stone and ceramic processing, glass processing, metal processing, track traffic, mechanical equipment, marine, stainless steel, pressure vessel, metal plate, power equipment, concrete cutting, composites processing and other areas.
- Competitive Advantages
- 1. Compared with traditional cutting methods, waterjet cutting has many advantages. The details are as follows.
- 1) Comparison of Water Jet Cutting and Plasma Cutting
- Plasma cutting has obvious heating effect and low precision. The cutting surface is hard for secondary operation. Water cutting belongs to cold cutting. It will not create any thermal distortion. The cutting surface is fine and it is easy for secondary operation.
- 2) Comparison of Waterjet Cutting and Linear Cutting
- Linear cutting has higher precision in metallic processing but the cutting speed is very slow. Sometimes, perforation, threading and other methods are needed before linear cutting. The cutting size is restricted. Waterjet cutting machine can punch and cut almost all materials with higher cutting speed, about 20 to 30 times faster than linear cutting. It also has a wide range of processing sizes.
- 3) Comparison between Waterjet Cutting and Laser Cutting
- Laser cutting machine requires large investment and it is usually used to cut steel sheet. It features high cutting speed and high precision. However, this cutting method will produce arc trace in the cutting joint and result in heat effect. Besides, it is not suitable for cutting some materials, such as some non-ferrous metals like aluminum, copper, alloy, etc. When the material is thick and hard, laser cutting is difficult or can’t finish cutting perfectly while waterjet cutting performs well. It is featured with low investment and running cost, wide application scope, high efficiency, easy operation and convenient maintenance.
- 4) Comparison of Waterjet Cutting and Other Cutting Methods
- a. Punching shear technique is applicable to some metal parts. It features high efficiency and high speed. However, special moulds and cutters are required. Compared to this cutting method, waterjet cutting has better flexibility. It can process work pieces of any shape at any time.
- b. Flame cutting is also a common method to process metals. It has a large range of cutting thickness, but it has an obvious heating effect. In addition, its surface cutting quality and precision is lower than that of waterjet cutting. Water jet cutting performs well in the cutting of high melting point materials, alloys and composites, etc.
- c. In glass, stone and ceramics cutting areas, the traditional method is to use diamond tool. It can finish cutting, sawing and milling operations with large range of cutting thickness and high cutting speed. But for those plates with normal thickness, waterjet cutting can give any curve cutting with high precision. Additionally, it has high rate of finished products. It also reduces the production cost and increases the added value of cut products greatly.
- 2. Features
- 1) Waterjet cutting machine is capable to cut metals like stainless steel, steel, copper and aluminum. It is also suitable for cutting strengthened glass, stone, ceramic, plastic and composite materials.
- 2) It will not generate heat and leave no arc trace on the cutting edge.
- 3) Waterjet cutting can give any curve cutting at high precision. No mould is required.
- 4) The cutting seam is very small, only 1 mm. The cutting surface is smooth. The roughness is from 3.2 um to 1.6 um.
- 5) No special clipping is needed for work pieces. Therefore, the operation is very easy.
- 6) Waterjet cutting machine can cut metal sheet with thickness of 200 mm.
- 7) It produces no heat damage to work piece’s surface or edges.
- 8) Together with a processing center, our water jet cutters can complete the operations like drilling, cutting and sawing in one time.
- 9) Distance between nozzle and work piece affects the size of the kerfs and the removal rate of material. Typical distance is 0.125" (3.175 mm).
- 10) Waterjet cutting machine makes a taper less than one degree on most cuts, which can be reduced or eliminated entirely by slowing down the cutting process.